مسیر ذوب و انجماد در جریان جوشکاری
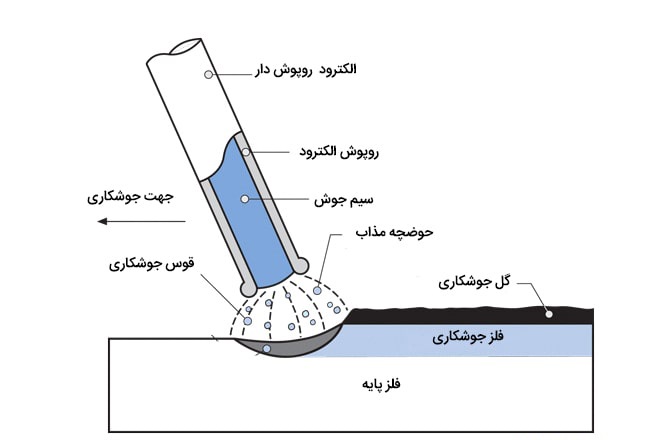
در کلیه فرآیندهای جوشکاری ذوبی یا مقاومتی یک منبع قدرت وظیفه تامین حرارت و افزایش دما را بر عهده دارد . حرارت حاصل به صورت افزایش دما سبب امتزاج فلزات پایه و در بعضی موارد الکترود یا سایر مواد مصرفی پرکننده در یکدیگر میشودو این پدیده خود را به صورت قوس الکتریکی شعله و یا مقاومت الکتریکی نشان می دهد. حرارت ورودی همیشه یک پدیده ی مثت و مفید نیست بلکه در برخی زمان ها جوشکاری موجب بروز مشکلاتی هم می شود . بنابراین در بررسی مسیر ذوب و انجماد در جریان جوشکاری باید تمامی فواید و مضرات ناشی از اثرات گرمایی را نز در نظر گرفت .در این راستا به تعریف مفاهیم اصلی در مورد اثرات منع قدرت حرارتی ومسیر انجماد جوش پرداخته خواهد شد.
میزان حرارت ورودی
میزان حرارت ورودی به طور مستقیم به منبع قدرت تولید حرارت و مکانیزم انتقال و راندمان انتقال حرارت از منبع به قطعه کار بستگی دارد. براین اساس می توان ادعا کرد که میزان حرارت ورودی به جوش به ترتیب در جوش های قوس الکتریکی و جوش های شعله ای و حجوش های مقاومتی کمتر خواهد بود. تنظیم پارامترهای جوشکاری در هر یک از فرآیندهای گفته شده به عنوان عوامل اصلی کنترل کننده ی منبع قدرت یا حرارت ورودی مطرح می باشد.
حداکثر دما یا درجه حرارت
مقدار حرارت ورودی را همواره باید به گونه ای تنظیم کرد که مقدار آن از میزان حرارت تلف شده ناشی از اتصال و توزیع حرارت تلف شده ناشی از اتصال و توزیع حرارت در سطح فلز بیشتر بوده و امکان رسیدن به یک حداکثر دما برای ذوب شدن قطعه کار را فراهم نماید. این مورد در فلزاتی که از ضریب انتقال حرارت خیلی بالایی برخوردار نیستند کار آسانی است و از طریق محاسبه یا تجربه قابل انجام است . اما در فلزاتی مثل مس یا آلومینیوم که حرارت را به سرعت در سطح خود توزیع می نمایند چنان چه منبع تولید حرارت ضعیف باشد فلز پایه ذوب نشده بنابراین باید از منبع حرارتی قوی تر پیشگرم کردن و سایر مقدمات استفاده کرد.
زمان باقی ماندن در درجه حرارت حداکثر یا نقطه ذوب
بسته به فاصله از مرکز اعمال حرارت و نیز میزان انتقال حرارت قطعه کار زمان باقی ماندن در دمای حداکثر در نقاط مختلف قطعه کار و زمان باقی ماندن در دمای حداکثردر نقاط مختلف قطعه جوشکاری شده متفاوت است. به طور کلی فقط 30 تا 70 درصد تولید شده توسط منبع قدرت به قطعه کار انتقال داده می شود. از این مقدار نیز فقط 40 تا 50 درصد به مصرف ذوب کردن محل اتصال می رسد و بخش بیشتر آن به مناطق کناری جوش هدایت شده آن جا را تحت تاثیر درجه حرارت قرار می دهد . بر این اساس درجه حرارت در نقاط مختلف فلز پایه در هنگام جوشکاری را میتوان به صورت منحنی های توزیع درجه حرارت در طول قطعه کار نشا داد.
هرچه قدر حرارت ورودی آهنگ ورود حرارت و سرعت سرد شدن بیشتر باشد و یا منبع توزیع حرارت به صورت متمرکز یا نقطه ای عمل کند منحنی توزیع حرارت فشرده تر و بعد توزیع حرارت و زمان باقی ماندن دردرجه حرارت حداکثر را به ترتیب زیر معرفی نمود:
-ولتاژ قوس الکتریکی
-شدت جریان قوس الکتریکی
-ضریب هدایتی حرارتی قطعه کار
-ضریب نفوذ حرارتی قطعه کار
-میزان پیشگرمایی
-ضخامت قطعه کار و
-سرعت جوشکاری
آهنگ سرد شدن
سرعت سرد شدن جوش یک از مهمترین پارامترهای موثر در بررسی فرآیند انجماد حوضچه جوش به شمار می رود. سرعت سرد شدن جوش در حقیقت متاثر از عوامل مهم زیر است:
الف) شکل حوضچه جوش
ب) حجم حوضچه جوش( اندازه حوضچه جوش)
پ) درجه حرارت حوضچه جوش
ج) حجم سرباره
چ) گاز محافظ(شدت جریان و نوع گاز)
ح) پلاریتی جریان جوشکاری
خ)ضخامت قطعه کار
د) طرح اتصال و فیکسچر و نگه دارنده یا مبردها و
ذ) درجه حرارت پیشگرمایی و زمان آن
هرچه سرعت ورود حرارت بالاتر باشد سرعت یا آهنگ سرد شدن کندتر است و در نتیجه حوضچه جوش بزرگتر می شودو پس میتوان اینگونه بیان کرد که بین اندازه حوضچه جوش و سرعت سرد شدن رابطه معکوسی وجود دارد . علاوه بر این ها اگر شدت جریان و ولتاژ به نحوی تنظیم شود که شکل حوضچه جوش تغییر نکند درآن صورت حرارت ورودی بیشتر سبب کند شدن سرعت سرد شدن در نتیجه وسیع تر شدن منطقه تحت تاثیر حرارت قرار گرفته جوش در کناره ها می گردد. عامل مهم دیگر ضخامت قطعه کار است . هرچه ضخامت قطعه کار بیشتر باشد نرخ سرد شدن آن در جوشکاری کمتر خواهد بود . علاوه برآن باید به طرح اتصال نیز توجه کافی داشت.
اگر این چهار نوع جوش از نظر سرعت سرد شدن بررسی شوند نتایج زیر بدست خواهد آمد:
- سرعت بالای سرد شدن :جوش گوشه مقعر به دلیل تماس بیشتر با فلز پایه و انتقال حرارت از سه طرف.
- سرعت متوسط سرد شدن : جوش تخت به دلیل انتقال حرارت از دو طرف.
- سرعت کمتر سرد شدن : به دلیل اتقال حرارت فقط از یک طرف
همچنین در جوش های چند پاسی آهنگ سرد شدن پاس یک کندتر از پاس های پرکننده است. که این امر نیز تا حدود زیادی به زاویه پخ و طراحی اتصال در محل ریشه جوش بستگی دارد .
حداقل دما یا درجه حرارت در انتهای کار
پس از انجماد حوضچه مذاب و رسیدن به دمای محیط در حقیقت نقطه پایان سرد شدن فرا میرسد . رسیدن به حداقل دما یا دمای محیط به شیب حرارتی فلز و جوش بستگی مستقیم داشته و تابع همان عواملی است که در مورد آهنگ سرد شدن بیان شد.
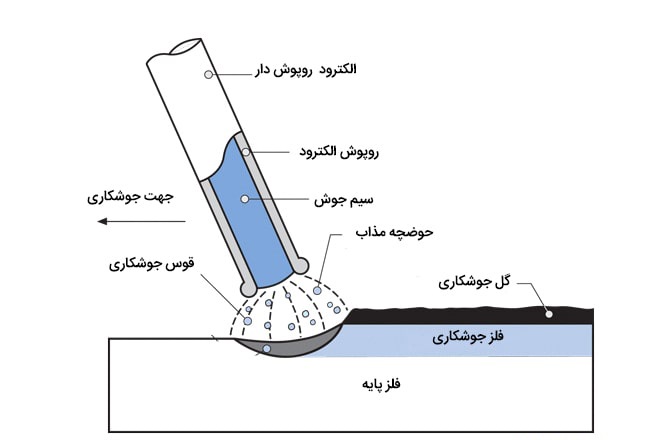
اولین دیدگاه را ثبت کنید